Производитель ПНД труб для защиты электрокабелей, водоснабжения, газопровода и канализации.
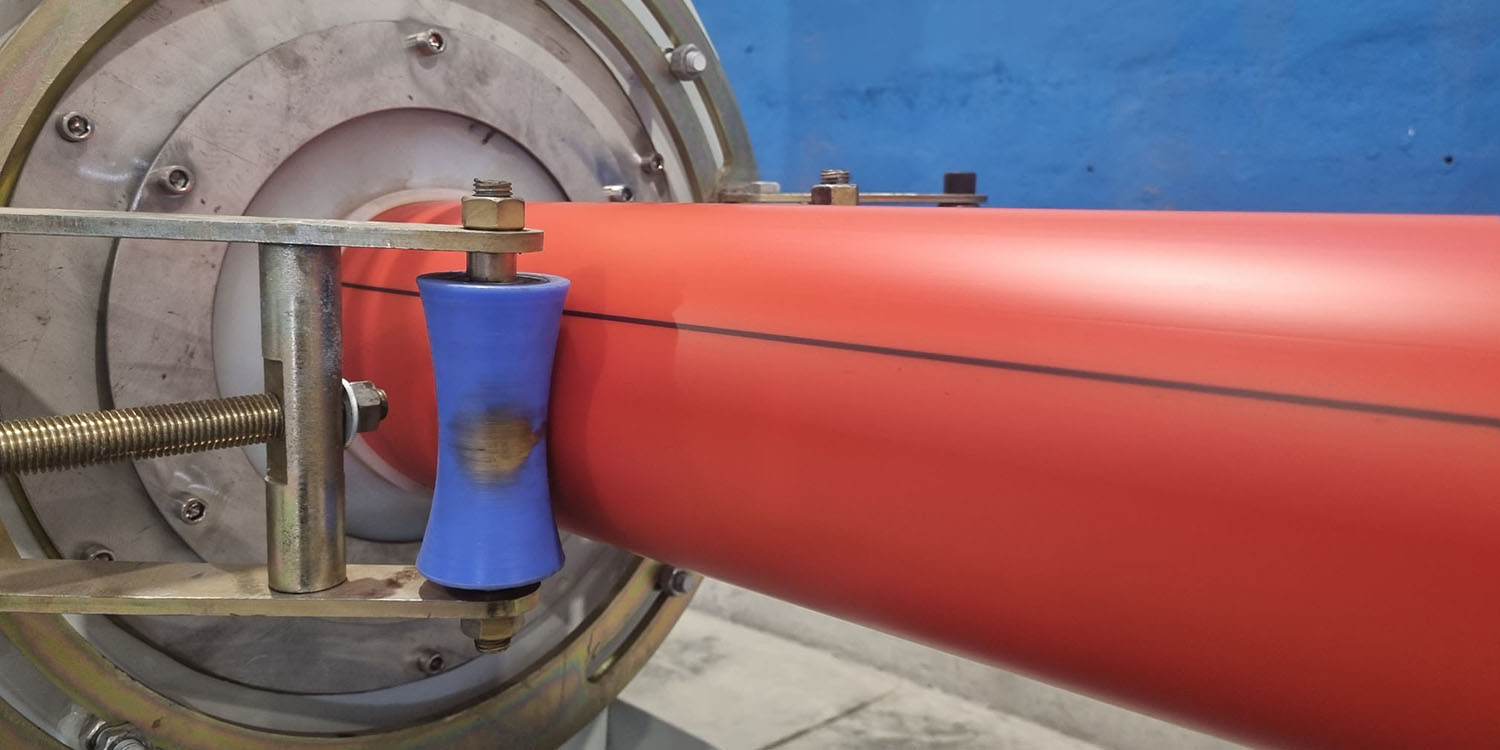
Технологический процесс изготовлеение пластиковых труб
1. Подача сырья
Сырье (гранулированный ПЭ 100) поступает на предприятие в мешках по 25 кг.
Предварительно сырьё засыпается в приемный бункер, откуда с помощью вакуумных загрузчиков подаётся в сушильный бункер где сушится подогретым воздухом.
Из приёмного бункера материал подаётся в экструдеры.
После сушки гранулы попадают в систему смешивания и дозирования, состоящую из набора приёмных бункеров, агрегатов смешивания и вакуумных насосов, соединенных между собой трубами. Система полностью работает автоматически, обеспечивая точное дозирование красителей и других добавок, а также хорошую смешиваемость.
Система смешивания состоит из нескольких агрегатов, каждый из которых готовит смесь материала для своего слоя многослойной трубы. Из системы смешивания подготовленный гранулят попадает в приемные бункеры многослойной линии, в которых также происходит окончательное досушивание. Далее материал проходит весы системы гравиметрии и попадает непосредственно в загрузочное отверстие шнеков.
2. Нагрев сырья и перемешивание
В экструдерах происходит нагрев гранул и перемешивание материала шнеком до однокомпонентной массы.
3. Доставка массы в форму
Гомогенная гранулированная смесь базового полимера (ПЭ) включает в себя добавки, вводимые на стадии производства в концентрациях, необходимых для обеспечения изготовления труб заявленного качества.
Шнек доставляет готовую массу в формовочную голову. Данная формовочная голова подразумевает собой выпуск трехслойных труб. Загрузка в каналы формовочной головы производится из четырех экструдеров:
4. Формирование трубной заготовки
Получение расплава полиэтилена осуществляется в экструдере, основным рабочим органом, которого является шнек, вращающийся в неподвижном цилиндре. Обогрев экструдера производится при помощи электронагревальных элементов. Цилиндр и инструмент разделены на несколько тепловых зон с самостоятельной автоматической регулировкой температуры каждой зоны. Для замера температуры используют термопары, установленные в стенки цилиндра и инструмента. Для предотвращения перегревов полимерной массы цилиндр экструдера охлаждается с помощью воздуха и воды. Регулировка охлаждения цилиндра осуществляется автоматически с помощью приборов тепловой автоматики.
Экструдеры через адаптер подсоединены к формирующему инструменту. Гомогенный расплав из каждого экструдера по кольцевым каналам внутри головы попадает каждый в свою полость и равномерно распределяется по диаметру.
Экструдер 25/25 осуществляет подачу материала для формирования маркерной полосы, идущей вдоль всей длины, на внешнем слое трубы.
5. Маркировка
Маркировочное устройство осуществляет нанесение на поверхность трубы наименование предприятия-изготовителя, наименование трубы, её марка, наружный диаметр, типоразмер, кольцевая жёсткость, максимальное усилие тяжения, длительно-допустимая температура эксплуатации, наименование нормативной (технической) документации, номер партии, содержащий дату изготовления, и номер смены.
Также маркировка содержит в себе персональный QR-код, через который при переходе по ссылке будет отражаться вся необходимая информация о конкретной партии изделия, включая паспорт качества и сертификат соответствия.
6. Отвод трубы
Отвод трубы производится при помощи специального, предназначенного для этого, тянущего устройства.
7. Отрез трубы
Далее труба проходит в отрезное устройство, где, в зависимости от выставленной длины отрезка, происходит отрезание трубы. Приспособление работает автоматически.
8. Упаковка и хранение
После отрезного устройства труба выходит на пневматический опрокидывающий стол, который откидывает её на временный склад хранения, либо наматывается в бухты в зависимости от заказа.
Упаковка (увязка) труб и формирование пакетов с ними осуществляются согласно распространяющейся на них нормативной и технической документации.
9. Контроль продукции
Далее осуществляется приёмка продукции ОТК и отправка на основной склад.
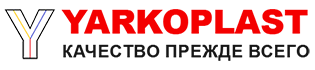
ООО "Ярковский промкомбинат"
Мы специализируемся на производстве и продаже высококачественных пластиковых труб, предназначенных для различных сфер применения.
Наша продукция соответствует современным стандартам качества, отличается прочностью и длительным сроком службы.
Свяжитесь с нами – мы предоставим подробную консультацию и поможем подобрать оптимальное решение для ваших задач.
Получите актуальный прайс-лист прямо сейчас!
Запрос прайс листа
Ваше сообщение было успешно отправлено